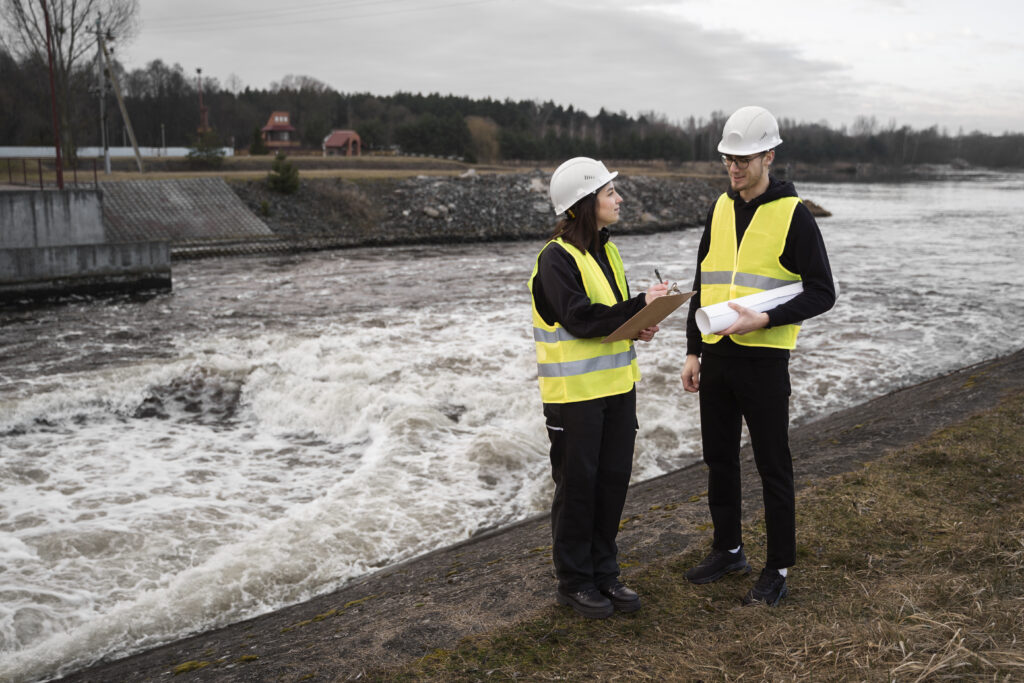
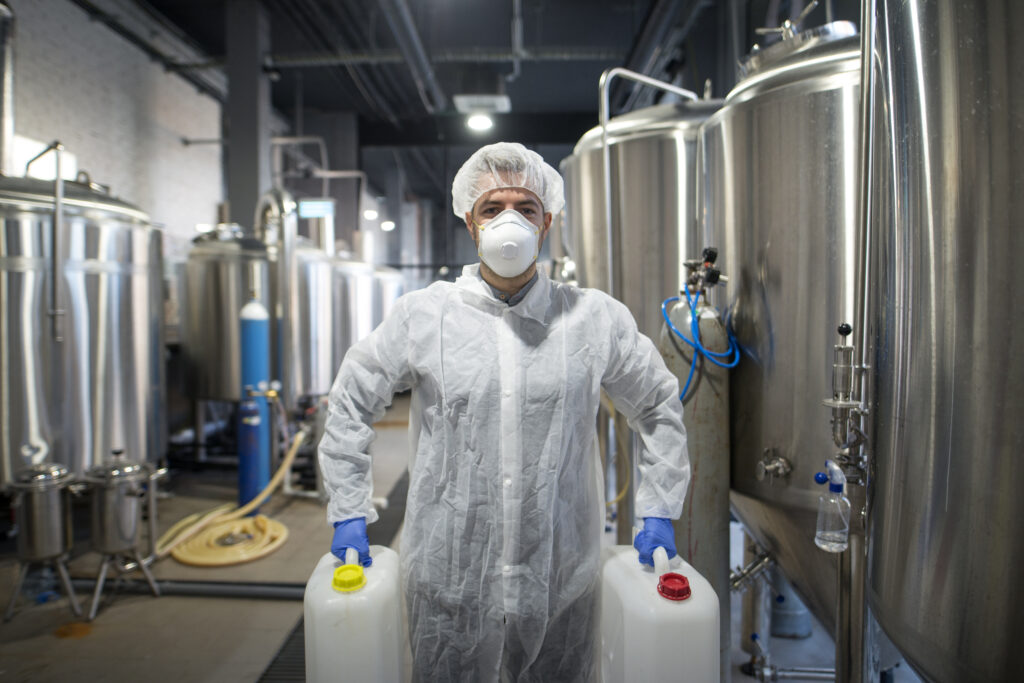
Water Treatment Chemicals
Cooling Water Program The Ionberg offer the wide range of chemical for Cooling water for prevention of corrosion, deposition and microbiological control. System components with high temperatures on heat-transfer surfaces are most vulnerable hardness deposits, predominantly the deposit consist of calcium salts. Corrosion can occur under inorganic deposits through differential aeration and under organic deposits – microbiological-induced corrosion (MIC) – due to the acidic nature of the biological processes or where skin temperature is too high. Heat exchangers that have process leaks are susceptible to organic fouling from poor microbiological control.
The Key Objective of a Cooling Water Program:
Performance: Failure due to improper chemical treatment can result in loss of production, equipment failure and large financial consequences.
Cost-Effectiveness: Optimizing the chemical treatment cost is always important.
- Scale and Corrosion Inhibitors
- Dispersant
- Biocides
- Bio-dispersants
- Alkalinity Reducers
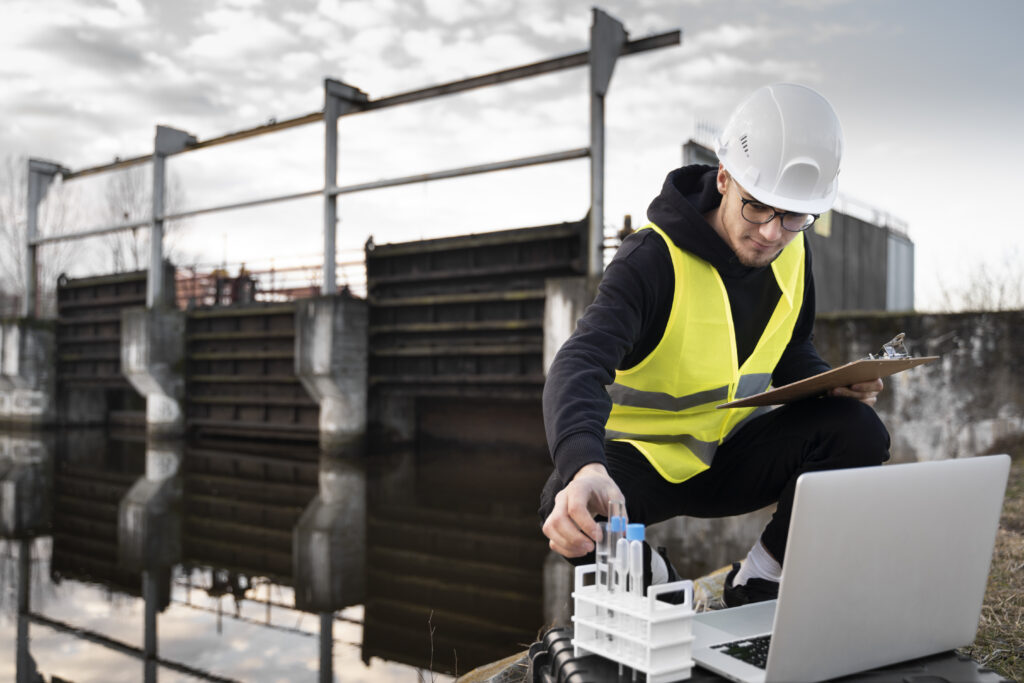
Boiler Water Chemicals The Ionberg provides wide range of Boiler water chemicals which is a combination of advanced polymers and organo-inorgano chemical treatment. The range of these chemicals includes :
- Scale and Corrosion Inhibitors
- Oxygen Scavengers
- Single Drum Treatments for Baby Boilers
- All volatile treatment for High Pressure Boilers
- Amine Based Condensate Treatments
- Sludge Conditioners
- Anti-Foaming Agents
- pH Boosters
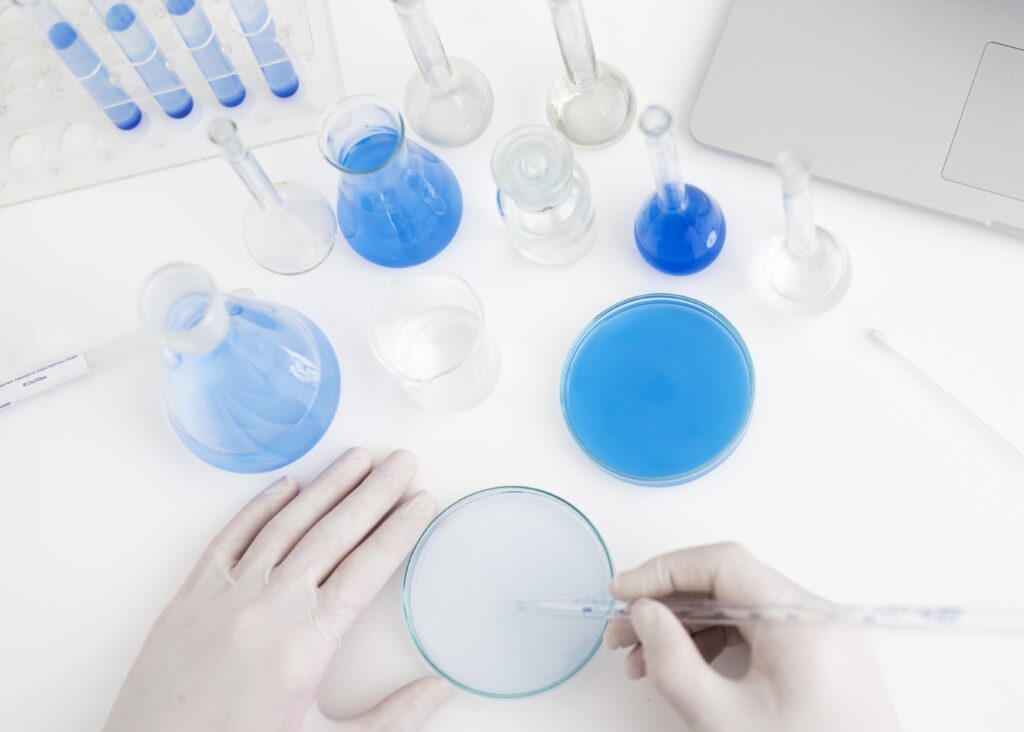
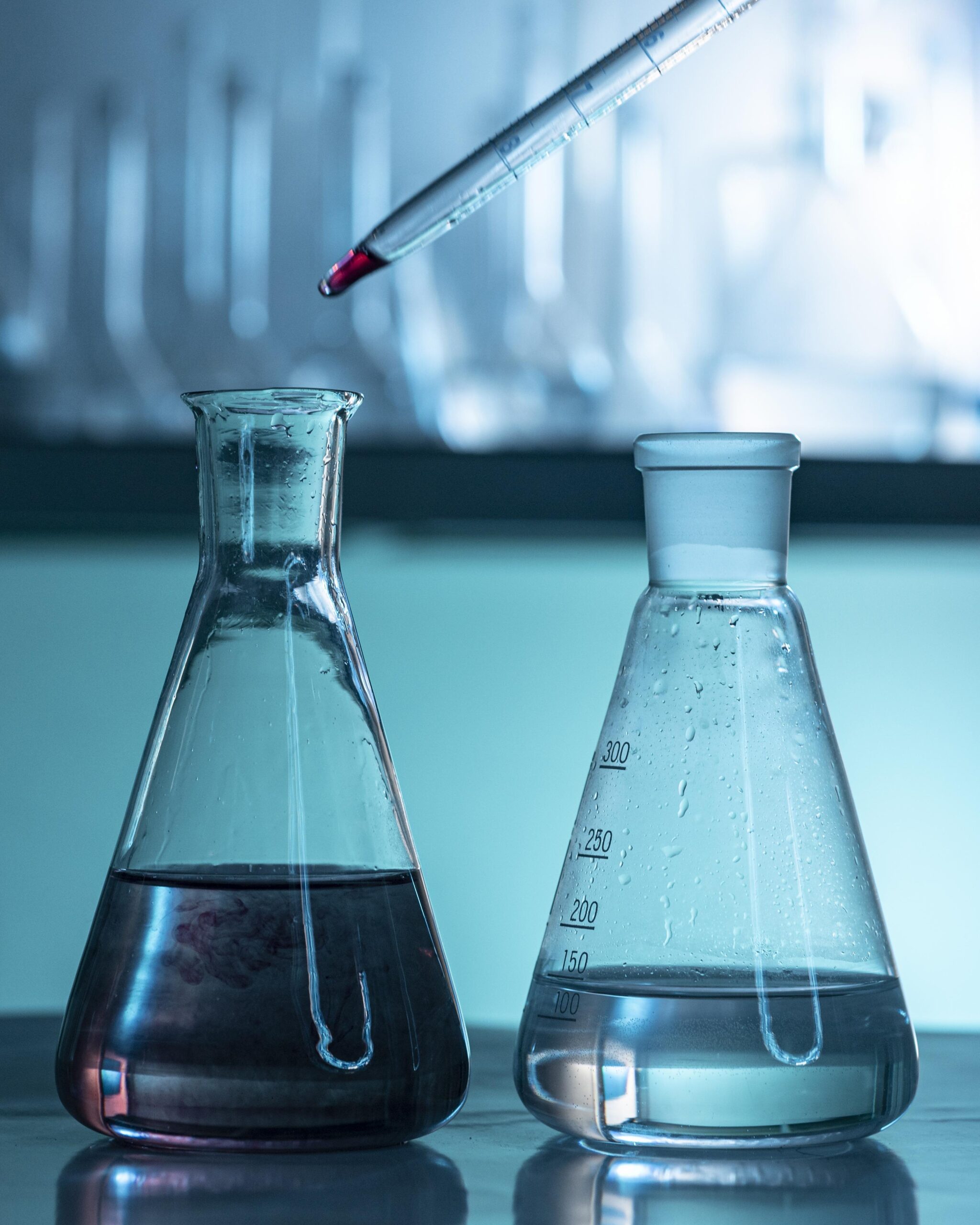
- RO Antiscalants
- Biological Treatment for Membrane Fouling
- Membrane Cleaning Agents
-
Miscellaneous Chemicals & Equipments
- De-Scaling Chemicals
- Poly-electrolytes
- Fuel Additives & Firesides
- Cleaner agent for AC Duct
- Membranes for RO
- Ion-Exchange Resins
- Media Activated Carbon
This range of chemicals comprises of:
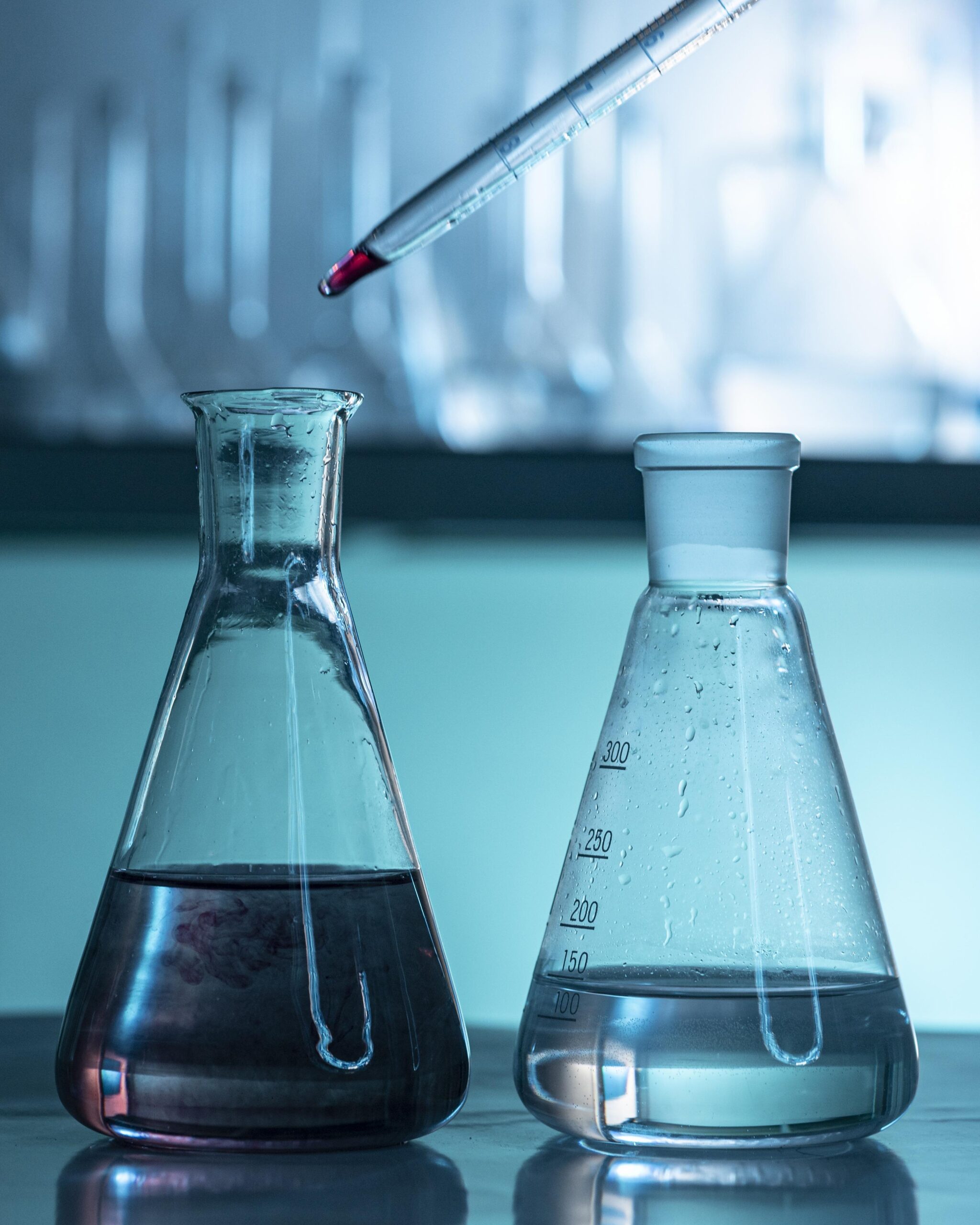
- RO Antiscalants
- Biological Treatment for Membrane Fouling
- Membrane Cleaning Agents
-
Miscellaneous Chemicals & Equipments
- De-Scaling Chemicals
- Poly-electrolytes
- Fuel Additives & Firesides
- Cleaner agent for AC Duct
- Membranes for RO
- Ion-Exchange Resins
- Media Activated Carbon
This range of chemicals comprises of: