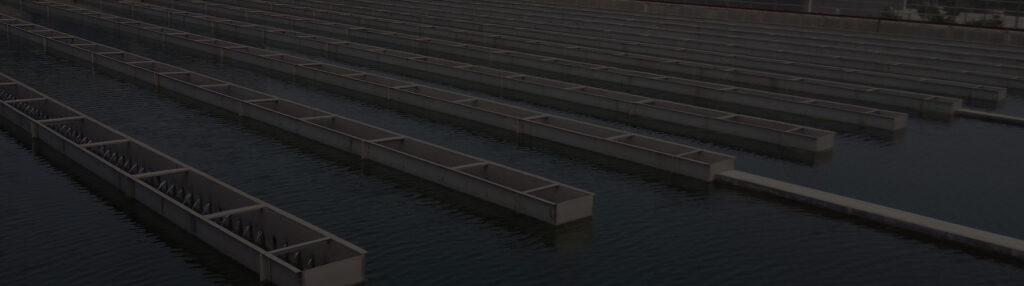
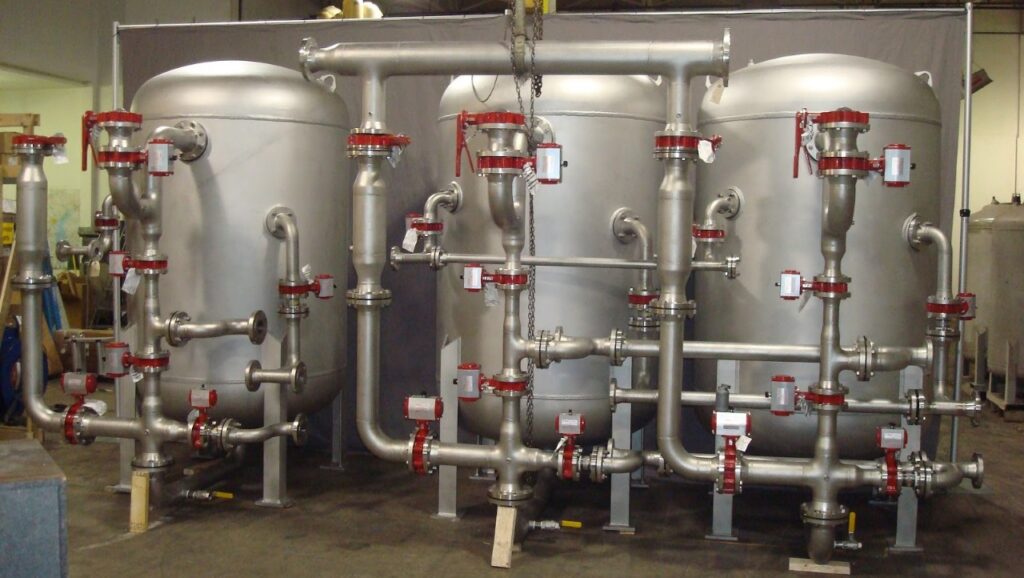
Condensate Polishing Unit (CPU)
Condensate Polishing Unit The Ionberg Condensate polishing is employed for purifying return steam condensate. This is essential for meeting the quality requirements of high pressure thermal cycles. It also minimizes consumption of make-up water. Condensate polishing is applied in places where the condensate is the major portion of the Boiler Feed Water. It is also applied if the risk of contamination of return condensate is persistent. The Condensate Polishing removes following types of impurities: Corrosive impurities Oxides of iron, copper and nickel are the major corrosive products. These products could be either in the form of particulate matter or in solution. They are removed by filtration of the condensate. Cartridge or precoat filters can be used for filtering these corrosive products. Dissolved Salts Sometimes due to leakage of cooling water the impurities caused by dissolved salts arise. The use of ion exchange demineralizers these impurities can be cleared. For low-contamination levels mixed-bed ion exchangers are commonly used. Separate cation and anion exchangers can be used only when there is higher level of mineral contamination.
Working Principle Condensate Polishing Unit In various manufacturing unit or plant steam is generated and released for generating electricity. The steam after loosing its heat condensate back into water. While condensing steam picks lot of impurities from the environment which should be completely removed before using condensate again. The polishing unit that is employed for this impurity is condensate polisher that employs ion exchange resin bed to remove the contaminants. After resin is exhausted it is regenerated. On the basis of regeneration, condensate polishing systems can be of following types :
![]() | Mixed Bed External Regeneration |
![]() | Mixed Bed In-situ Regeneration |
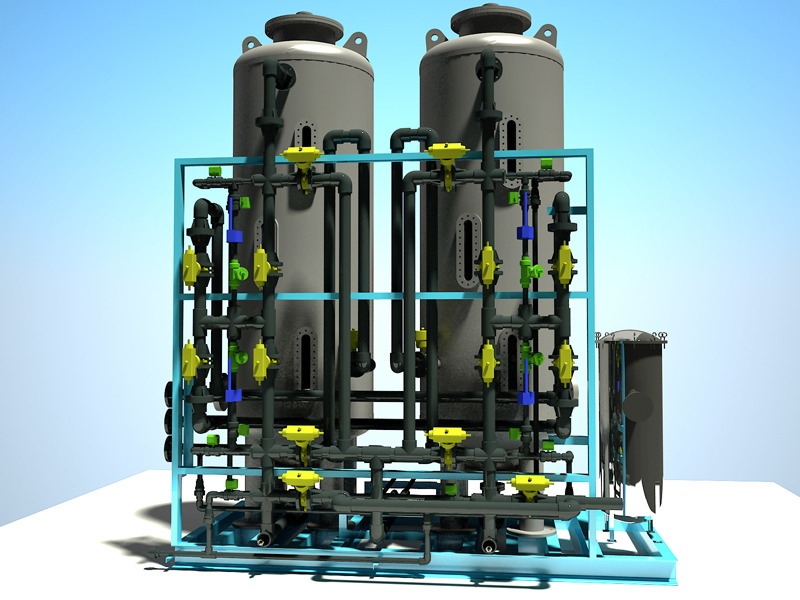
Feature of Ionberg’ s CPU
![]() | It should have good physical strength in order to withstand vigorous cleaning. It is also necessary for the rigorous of hydraulic transfer during regeneration. |
![]() | For effective separation of resin’s density should be precise. |
![]() | To prevent any flow restriction during operation, size and kinetics of the resins is also important. |