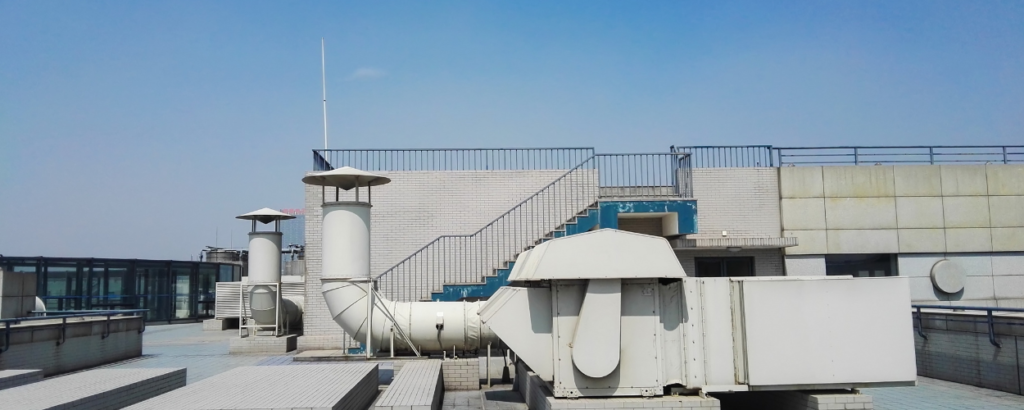
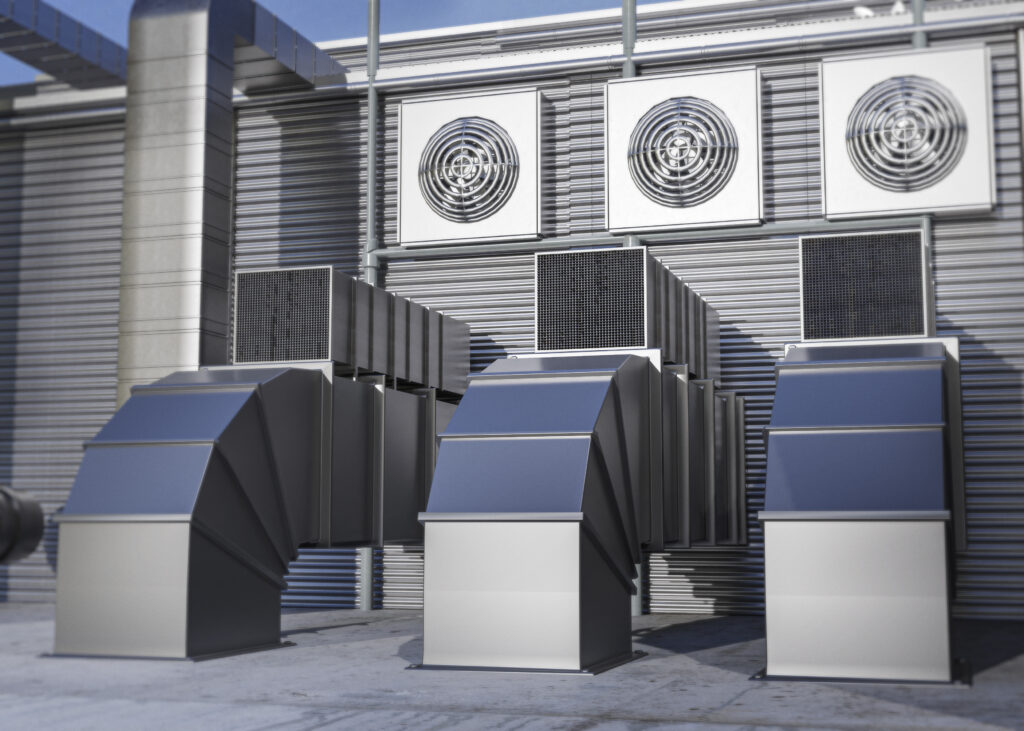
Air Pollution Control Equipment
Experience in the Design & Manufacture of air pollution control equipments and its accessories have been achieved with in-depth understanding of the process requirements and giving practical and optimal solutions. To ensure best results, we utilize the latest technologies. We follow standard work practices in manufacturing all our products, follow strict quality control procedures and timely deliver the materials to the utmost satisfaction of the customers. This experience has proven that tailoring air pollution control equipment to a particular application is an involved engineering process.
Application Industries
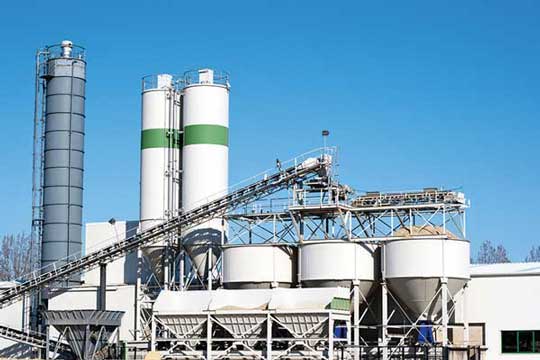
Cement
Cement industry utilizes Ionberg's air pollution control equipment for sustainable emissions reduction and environmental compliance.
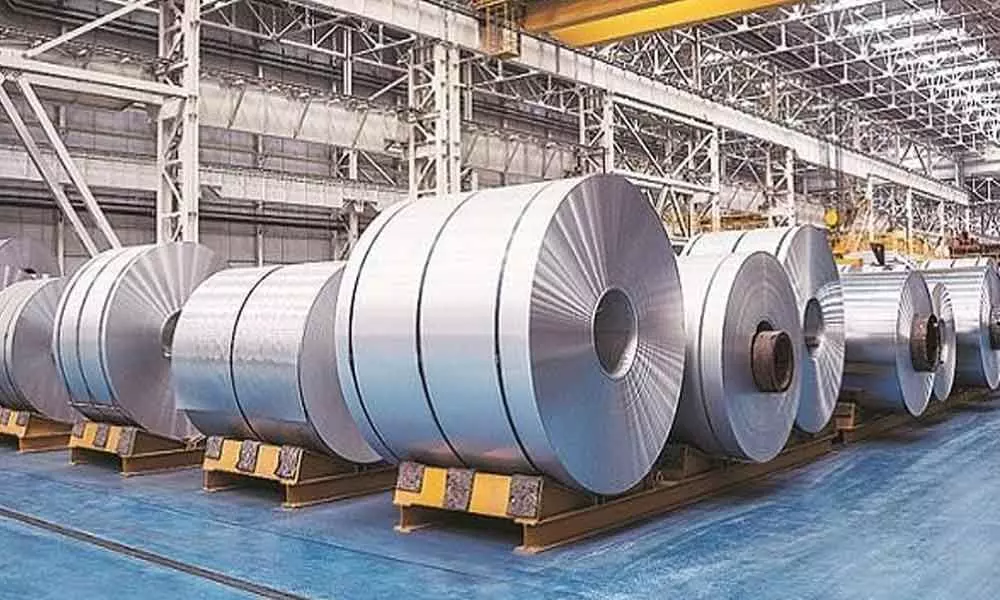
Steel
Ionberg's air pollution control solutions support steel industry sustainability, ensuring cleaner air and reduced emissions.
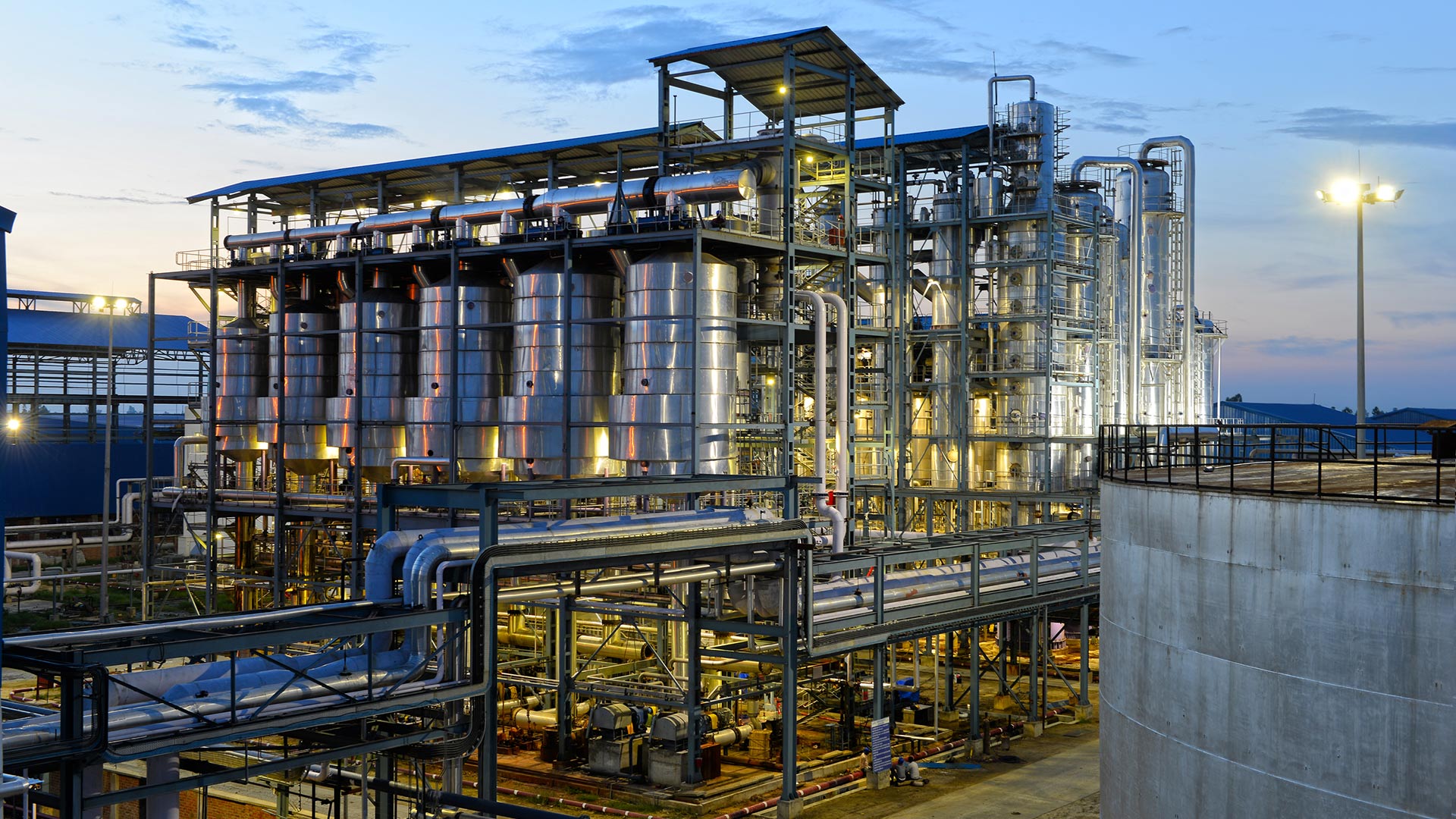
Sugar & Distilleries
Ionberg's air pollution control systems enhance sustainability in sugar and distillery industries, ensuring environmental compliance.

Paper&Pulp
Ionberg's air pollution control equipment enhances eco-friendliness in paper and pulp industry, reducing emissions and ensuring compliance.
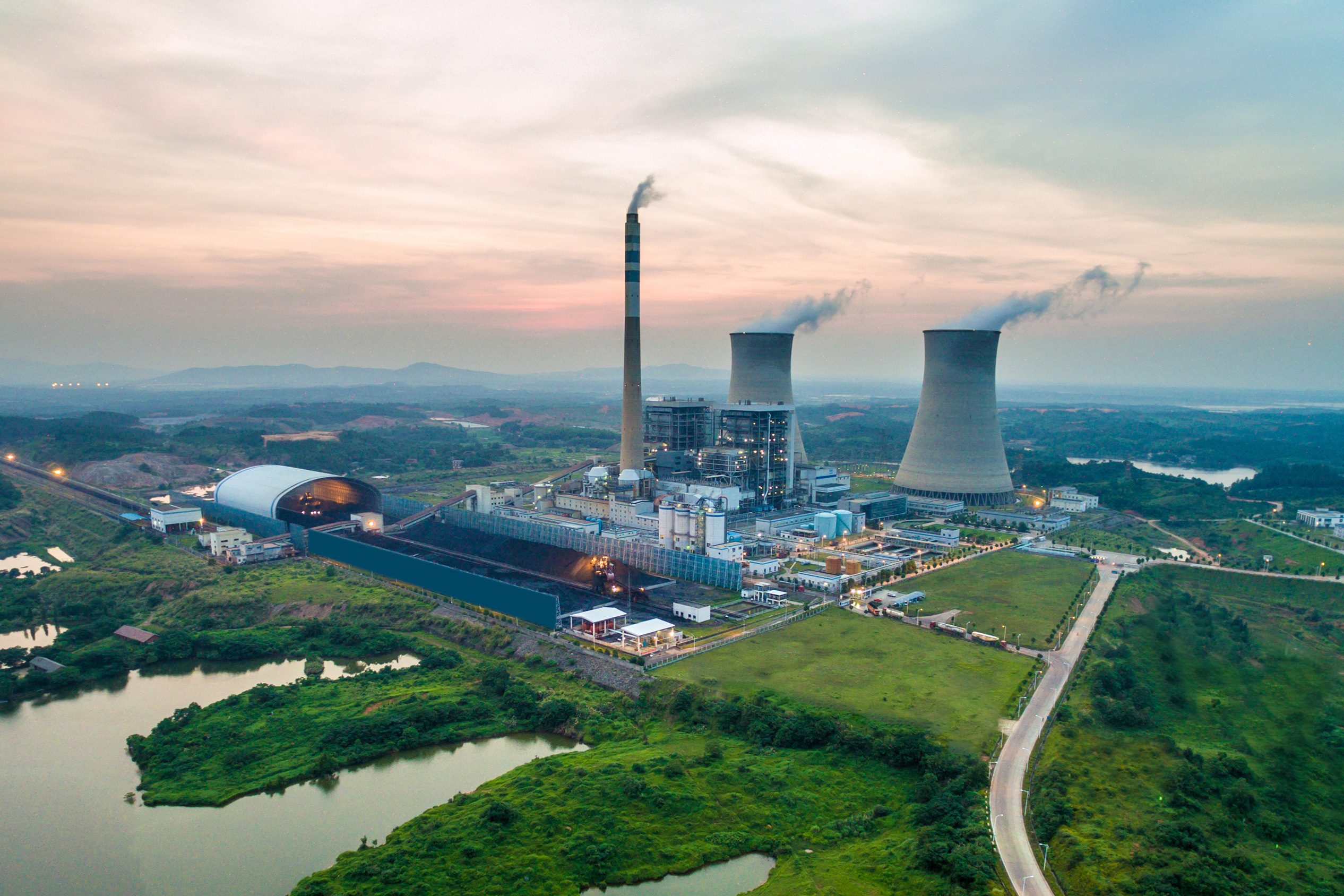
Power
Ionberg's air pollution control solutions optimize power industry emissions, fostering cleaner energy production and environmental compliance.
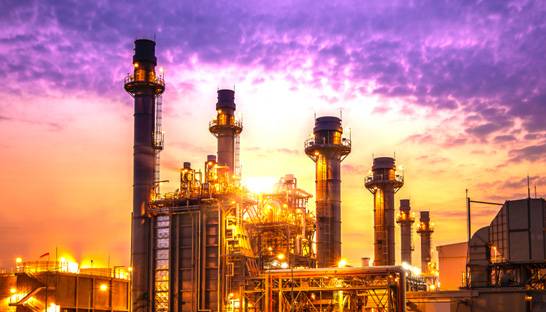
Chemical Industries
Ionberg's air pollution control systems ensure cleaner air and compliance with environmental regulations in chemical industries.
Reverse Air Bag House For cleaning of high temperature gases reverse air bag houses are widely used in the industry. Compared to the high pressure cleaning systems, the reverse air cleaning system used in RABH is most suitable for Woven and fragile high temperature filter media like fiber glass which can withstand operating temperatures of 230 – 250 Deg C. RABHs are offered with offline cleaning systems and hence normally will be in modular constructions. The Ionberg RABHs are offered with both normal fiber glass bags and with fiber glass PTFE membrane filter media. The optimal air to cloth ratios are selected depending on dust concentrations and type of filter media. RABH for Cement Kiln / Raw Mill exhaust gases Gas Distribution: Inlet & outlet plenums are designed ensuring uniform gas distribution across all the modules. To ensure the uniform gas distribution, CFD studies are carried out using software tools like FLUENT, ANSYS etc. Casing & Hoppers: Casing, Hoppers etc are designed and manufactured and are fully leak proof thus avoiding the ingress of false air. The valley angle of hoppers is maintained for easy disposal of collected dust. Filter Bag Cleaning: RABHs are offered with offline cleaning wherein one module is under cleaning and other modules are in filtration mode. Each module is provided with inlet butterfly damper and outlet puppet damper to ensure isolation during the cleaning cycle. All the puppet dampers are operated pneumatically through a control panel.
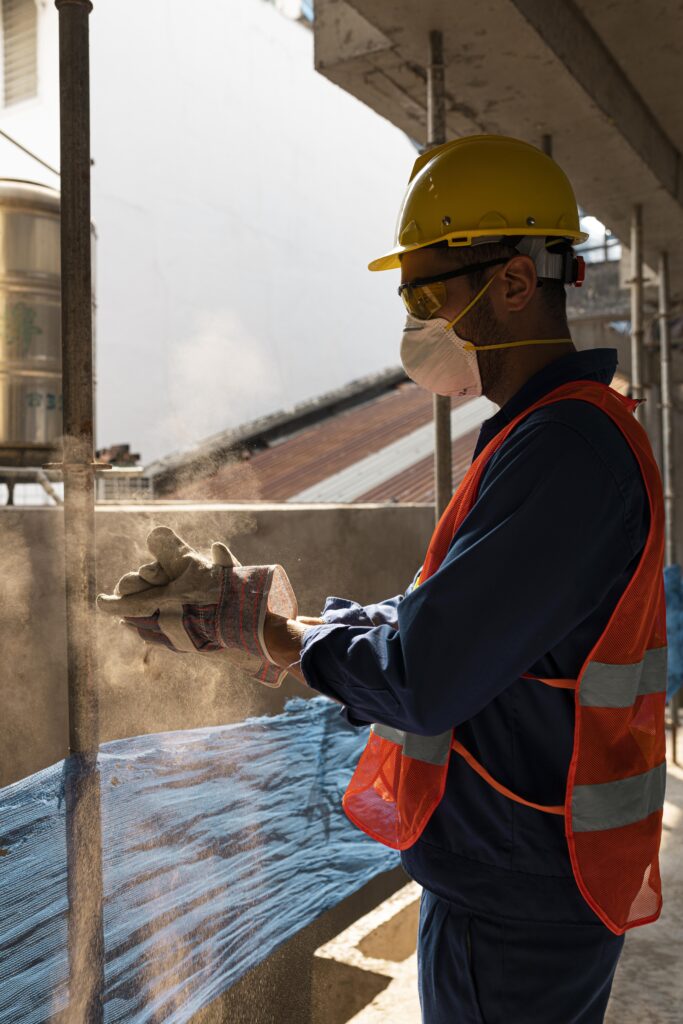
Temperature Control: The Ionberg has capability to design manufacture and supply large size RABHs. It has supplied RABHs with a gas handling capacity of 4, 00,000 Am3/hr to 13,50,000 Am3/hr at 220 – 240 Deg. C Salient Feature of Ionberg ESPs Discharge electrodes: Rigid Pipe & Spike discharge electrodes are made from deep drawn CRCA tubes, ensuring longer life by preventing breakage/snapping and ensures minimum arcing and allow considerable voltage resulting in higher efficiency . Collecting Electrodes: Collecting plates are made from CRCA sheets of 1.2 to 1.6 mm thickness having structural rigidity to maintain consistent electrode spacing which is very essential for performance of ESPs at high efficiency. Casing & Hoppers: Casing, Hoppers etc are designed and manufactured and are fully leak proof thus avoiding the ingress of false air.The valley angle of hoppers is maintained for easy disposal of collected dust. Rapper Design: The Rapping system is designed to produce sufficient acceleration for collecting and discharge electrodes to handle dust of any resistivity. The system is designed to facilitate adjustment of rapping frequency / cycles depending on requirement at site.Power Controls: Microprocessor based Transformer Rectifier Controllers respond automatically to changing precipitator operating conditions and provide maximum power at all times based on the programming designed for each application. The controllers have fully adjustable spark response control under-voltage / under-current control and alarm for component protection. Gas Distribution: Gas Dsitrubution Screens / Vanes are designed based on CFD studies carried out using software tools like FLUENT, ANSYS. Uniform gas distribution ensures maximum collection efficiency of ESP.